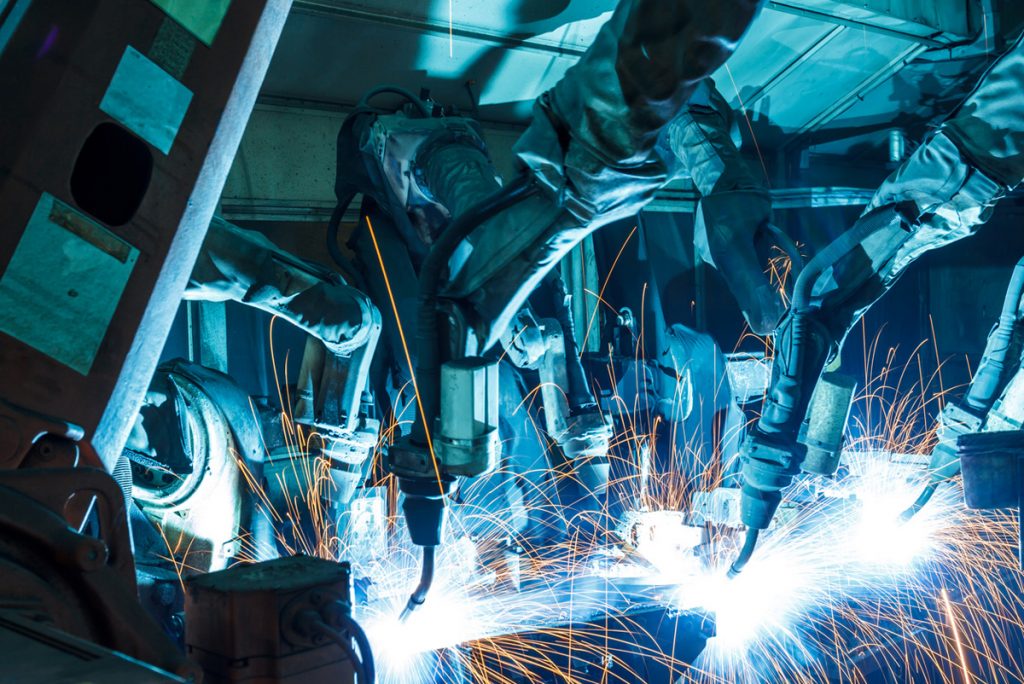
Digital Welding
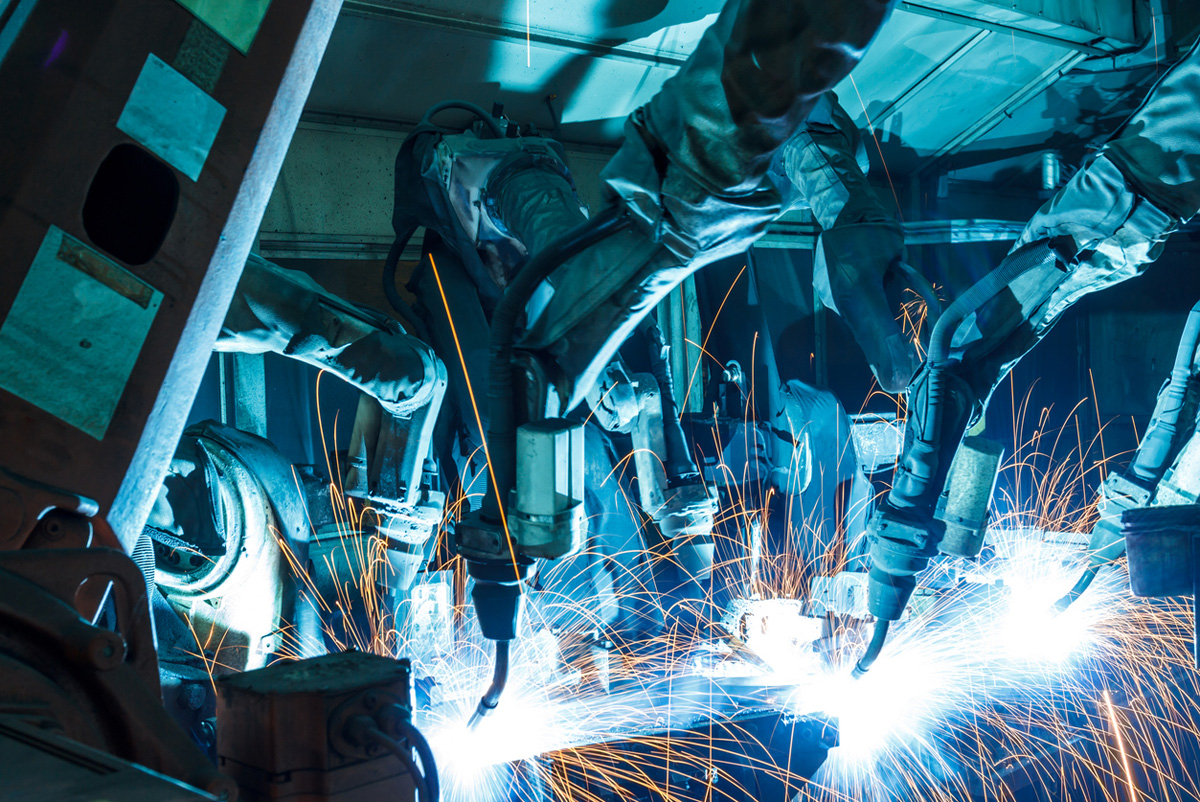
Digital Welding is the integration of digital technology to improve efficiency and control in welding. New techniques, automation and equipment create better and more consistent welds with reduced waste.
Since the invention of computers in 1950, every aspect of our daily lives has been speeding towards digitalisation. From precision engineering to basic tasks like opening curtains, technology is being developed relentlessly to reduce manual involvement and increase efficiency. Our world is heavily impacted by digitalisation, and welding is no exception. The ancient welding technique is being improved and enhanced with digital processes like predictive maintenance, automation, and weld monitoring. In this blog, we’ll examine the role of digital technology in welding.
The Future of Welding
From heating metal over charcoal fires in the Bronze Age to robotics and cobots in 2024, welding processes, equipment, and theories constantly evolve. Technological advances have had a huge impact on welding in recent years. Let’s take a look at some of the most significant innovations in this age-old process.
Augmented Reality Welding Helmets
Welding helmets are a critical piece of equipment for welders. Without them, the intense heat, flying sparks, UV rays and radiation would cause severe burns and irreparable damage to the eyes. Traditional welding masks and helmets are made from a non-flammable shield to protect the skin, with a darkened lens to protect welders’ eyes from the harmful light produced by the electric arc used to melt and join metals. The lens must be so dark that the welder can’t see anything until an arc is struck. In recent years, welding helmets have improved vastly through digitalisation. Augmented Reality helmets are a game changer in the world of welding. From within the helmet, a technician can view torch angle, welding parameters, work instructions and potential defects. Sensors detect the start of a weld and automatically adjust the lens accordingly. The introduction of Augmented Reality welding helmets has improved accuracy and safety and allowed less experienced users to repair welds successfully.
Laser Welding
Laser welding is a growing area in digital welding. The process uses a high-energy laser beam to join materials. It is extremely precise and highly efficient. Laser welding is so exact it can also be used to restore imperfections in metal; only the area with imperfection is affected, meaning the integrity of the remaining part is maintained. Laser welding doesn’t heat metal as traditional welding does, so it won’t introduce impurities or alter the material’s structure in the same way. The process is so cool that the metal can be handled with bare hands as soon as it’s been repaired.
Laser welding is suitable for cast iron products, too. It can successfully create strong welds and reduce cracking, and it’s an excellent option for hard-to-reach areas. However, laser welding does have significant disadvantages. It has a high initial cost, making the process very expensive and simply not cost effective for many applications. It also has limited penetration and struggles to weld particularly thick materials, or large gaps. Laser welding cast iron is more suited to thin or delicate parts while gas fusion remains the leading repair method for automotive parts, marine components, including cylinder heads, and industrial machinery.
Automation and Robotics
Robotic welding is a significant future trend in welding. Benefitting from artificial intelligence and machine learning, robotic arms perform welding tasks more efficiently and with increased precision. Each task is performed consistently, and even complex welds can be performed without human intervention, reducing the human error factor. This trend in welding is set to increase rapidly as robotic systems become smarter through machine learning.
IoT and Data Analytics Integration
The Internet of Things is a network of physical devices that can connect to the Internet and share data with other devices. Data analytics and the IoT are exciting developments in the welding industry, offering endless possibilities in terms of integration and control. Sensors can process real-time data on quality. Then, adjustments and improvements are automatically fed back to technicians. Multiple machines can work together, making complex industrial welding processes smoother and more efficient. This continuous monitoring and data collection vastly improves quality and consistency. Predictive maintenance schedules can also be deployed, reducing downtime and improving the lifespan of equipment.
For the welding industry, legacy processes and systems still dominate within the sector. But the outlook is promising as new innovations take hold.
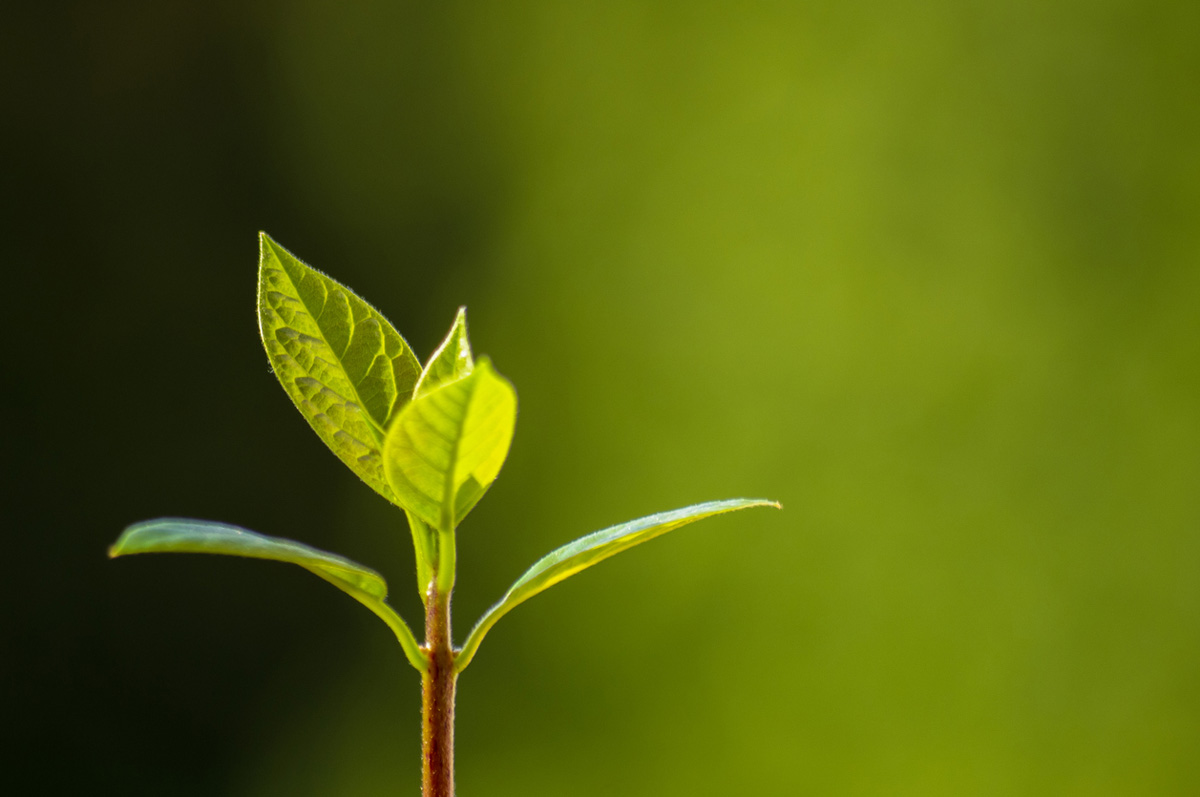
Eco-Conscious Welding
With the current focus on environmental issues and the pressure to act responsibly, it’s good to know that many of these advancements in digital welding have a positive impact on sustainability: laser welding requires less energy; automation, robotics, and the Internet of Things are more efficient and produce less waste; and predictive maintenance improves the longevity of equipment. The future of welding is bright.
If you have a damaged cast iron item, contact the team at Cast Iron Welding Services for an informal discussion. Through years of dedicated service to the cast iron industry, we have perfected our gas fusion welding process. Thanks to our work on unique, diverse projects up and down the country, we have extensive knowledge regarding cast iron repairs.